Imagine taking the Ducati desmodromic valve system and adding electronic control that provides brief bursts of two-stroke power!
The result could be a motorcycle engine that delivers great low-down torque as well as high-end power, without compromise.
British company Camcon Automotive has produced just such an engine.
They claim their electronic Intelligent Valve Actuation (IVA) system provides more power and torque, better fuel economy and lower emissions.
IVA also does away with timing belts and valve springs, so the engine would be lighter and, theoretically, less expensive to service.
While the project is a collaboration with Jaguar Land Rover, IVA has a lot of potential in motorcycles and would help save the internal combustion engine from being shelved by “clean” electric power.
The only drawback is they would make engines slightly more expensive to manufacture.
How Intelligent Valve Actuation works
The system uncouples the valves from the crankshaft and uses electronic motors to operate open and close miniature camshafts on each valve via a desmodromic mechanical system.
They say this gives them unlimited possibilities to open and close the valves in a variety of ways.
Camcon has just introduced a version of the IVA tech that runs in single-cylinder engines, but the system can also be used in any type of multi-cylinder engine.
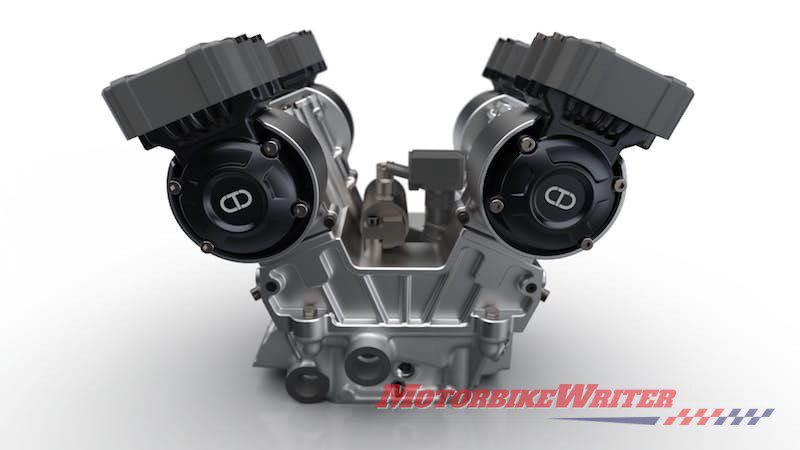
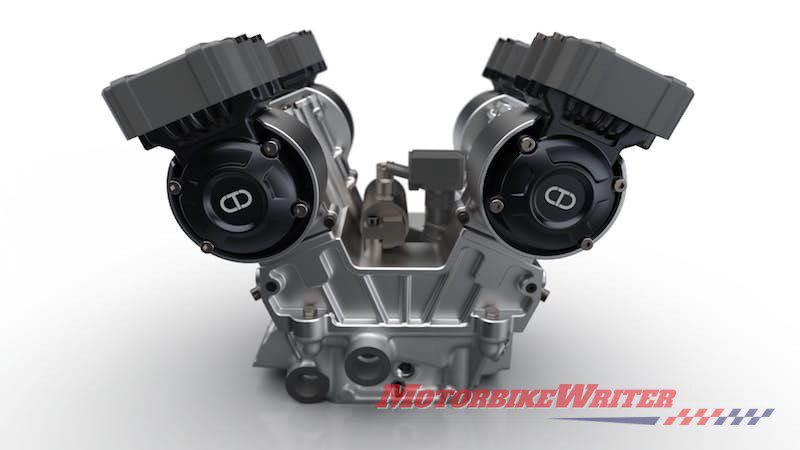
They have so far only used IVA on the inlet valves, but say it is also possible on the exhaust valves.
IVA monitors the position of the crankshaft to perfectly synchronise and control valve timing, lift and duration.
It goes way further than variable valve timing which Honda and Ducati have introduced to their motorcycles.
Camcon COO Mark Gostick says IVA is now possible because of modern electronics is economical, has the necessary processing bandwidth and can reliably tolerate hot conditions.